Precise pipeline inspections with thermal Camera
Pipelines are used to transport fluids such as liquids and gases, as well as liquid mixtures with solid particles.
Pipeline inspection with thermal camera is an important part of the effective operation of long-distance piping systems supplying variable media. Because the temperature of the transported media differs from that of the surrounding air, thermal cameras can provide a vital role in inspection and maintenance efforts.
By using thermographic systems, one can quickly detect and localize defects to pipeline insulation, as well as leaks. In some cases, leaks can even be detected and localized in underground pipelines.
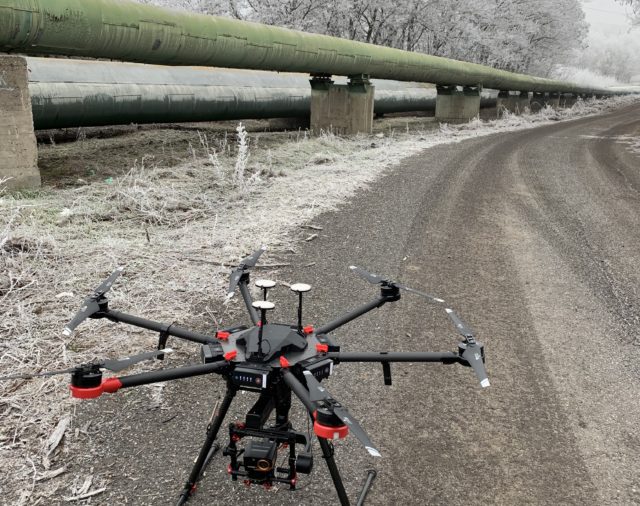
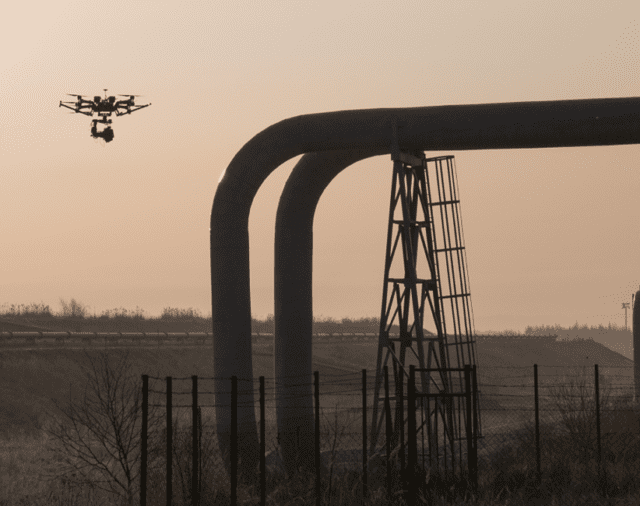
What is at Stake?
Thermo-diagnostic tools can aid in the operation and maintenance of a wide variety of systems: hot water piping, water mains, steam piping, product piping (crude oil or gas piping), piping in chemical operating units, the food industry, agriculture, power plants, mines, and more.
In most cases, pipelines do not only transport material – they supply heat energy to the transferred medium. This heat depends on proper pipeline insulation, which can be determined through the detection of pressure losses in pipelines. Thus, the whole transport system must be completely sealed because leaks of media are not only losses of mass, energy and profits, but often ecological losses as well.
Pipeline reliability can suffer because of poor design, improperly selected material, defective transport system construction, and unexpected conditions that arise during construction. This text deals with external piping systems that are permanently affected by atmospheric influences and are threatened by non-permitted interventions (mechanical damage due to lack of knowledge, accidents, or intentional actions).
Damage can emerge as a weakening of the cladding on the external insulation, as well as in leaks of heat energy, in addition to pipe breaks and losses of the transported medium. At the same time, risk arises from wear on the thickness of piping through internal corrosion (during the transport of aggressive liquids) and mechanical stressing (in the case of the transport of non-homogeneous materials with solid particles)
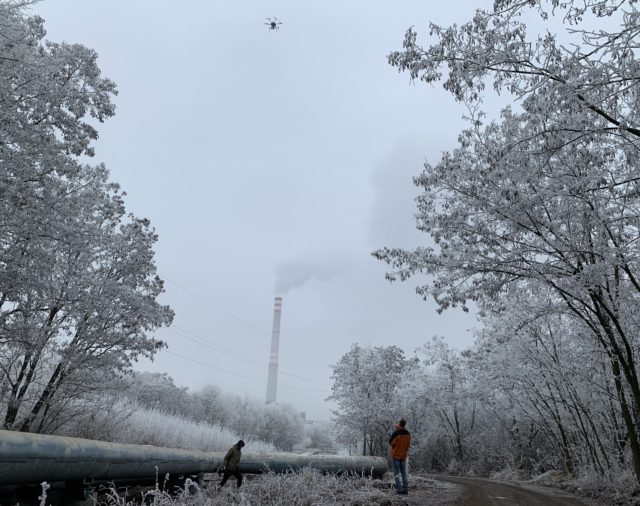
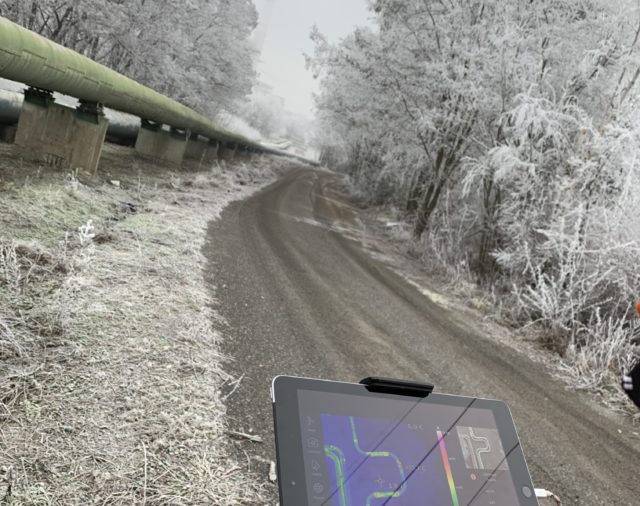
Airborne inspection of pipelines
Due to the risk posed by losses arising from piping defects, pipelines must be regularly and carefully inspected. Unfortunately, inspections bring their own risks.
Pipeline systems are often located underground. Above-ground pipelines often extend for hundreds of kilometers in areas where access roads are restricted and the surrounding countryside is impenetrable.
This can make access to pipelines incredibly difficult or impossible. It is simply not humanly possible to visually check every inch of piping, and built-in measuring systems (such as pressure meters and flow meters) are financially demanding and unreliable because even they cannot cover every high-risk area.
Luckily, an elegant and simple solution to the inspection problem facing long-distance pipeline operators is available. This is the utilization of a UAV equipped with a camera. Simply- it’s pipeline inspection with thermal camera and drone.
A drone can fly above the whole length of a pipeline while recording and displaying the monitored scene in real time to the inspector, who remains safe and sound.
The Workswell WIRIS
The Workswell WIRIS thermal imaging system is designed to be used with a drone (UAV). The set is light, mobile and fully controlled using a standard RC controller. The WIRIS system combines two cameras – a camera for the visible spectrum, for the inspection of visible defects on the piping, and a thermal camera, for detecting hidden defects. The servicing software enables remote switching between camera regimes, the recording of radiometric videos, and the creation of static images in the visible as well as the infra-red spectra. The operator sees objects under the drone in real-time, and they can also analyze their records to identify damaged areas.
The Workswell WIRIS thermal camera, unlike similar systems, enables users to manually set the temperature range, e.g. to the interval from 15 °C to 25 °C. Temperatures can even be changed mid-flight. This means that the settings can be quickly modified to achieve the correct thermal sensitivity setting without landing. This is necessary for the localization of minor hot water leaks below ground as well as for the most precise localization of large defects.
Measuring temperature automatically
Moreover, the system can be outfitted with a GPS sensor for storing location information on the position of the drone when it produced a given record.
The system measures temperature in the central point, as well as at the local minimum and maximum. The minimum and maximum are localized by blue (minimum) and red (maximum) crosses. This function can be used to navigate drones because the system automatically shows where the largest potential problem is located.
However, Workswell’s WIRIS also offers other functions suitable for this application: for example, continuous ZOOM (up to 14x for a thermal camera and 16x for a color camera) enables the exact localization of the problem. Similarly, control over NUC calibration guarantees that it is done at the right time.
Fully calibrated
Finally, the Workswell WIRIS system comes fully calibrated. During production, we check the precision of the temperature measurements taken by each unit, and include a calibration sheet with the stated precision of the measurement with each delivery. This ensures the accuracy of the thermal camera’s measurement results. And you are ready for accurate pipeline inspection with thermal camera.
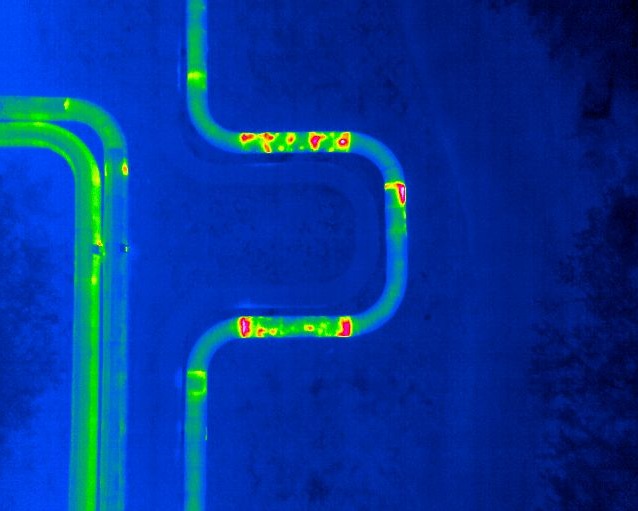
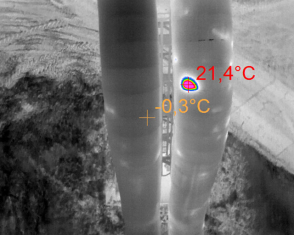

How detect a defect?
With this solution, the inspector enjoys an immediate overview of the condition of the pipeline. If a defect is detected, they can focus in at great detail and, if possible, personally check the area.
However, a traditional camera for the visible spectrum will only discover a fraction of potential pipeline defects, as it only records areas with visible damage or leaks. For example, a traditional camera cannot detect defects to internal heat insulation, nor leaks that occur below ground. And that’s why pipeline inspection with thermal camera cames with all benefits.
Safe lives and economics
Only with the timely detection of areas with thinning insulation and damaged cladding can major accidents that threaten the lives and health of the public – to say nothing of economic losses – be prevented. This is where a thermal camera comes in. Thermal cameras detect otherwise hidden defects and record the thermal radiation of the objects they record. These defects are identified on the basis of the difference between the pipeline’s surface and the experience of the operator. Thanks to the illumination of these divergences, it is easy to identify where the insulation is damaged, and spot where heat losses occur during the transport of heating media.
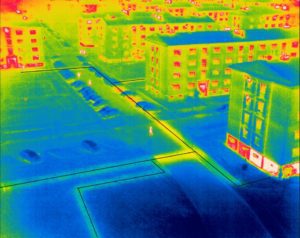
Discover problems easily
In the case of underground pipelines, the penetration of hot water causes the affected earth to heat up, so it is possible to discover where the pipeline is broken underground via thermal camera. This means that it is no longer necessary to excavate kilometers of pipelines to discover a single rupture. The different temperature of the background and thin areas means there is a risk of the pipe breaking, so timely intervention may well prevent fatal consequences.
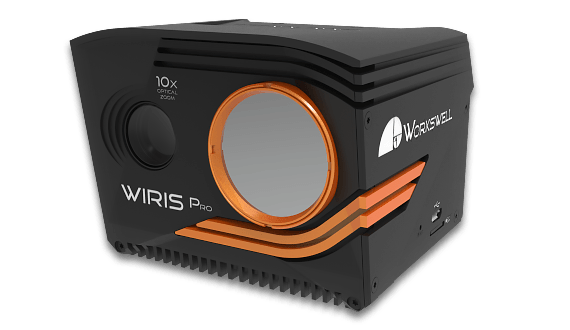
Thermal drone found underground pipeline leaks (about 1.5 meter)
During the thermal drone fly, temperature inhomogeneities were discovered at the points of expected leakage of hot water from the pipeline
Excavation works showed defects on the pipeline at a depth of about 1.5 m